Suction Wings Wind-Assisted Propulsion in the Marine Industry: An Overview
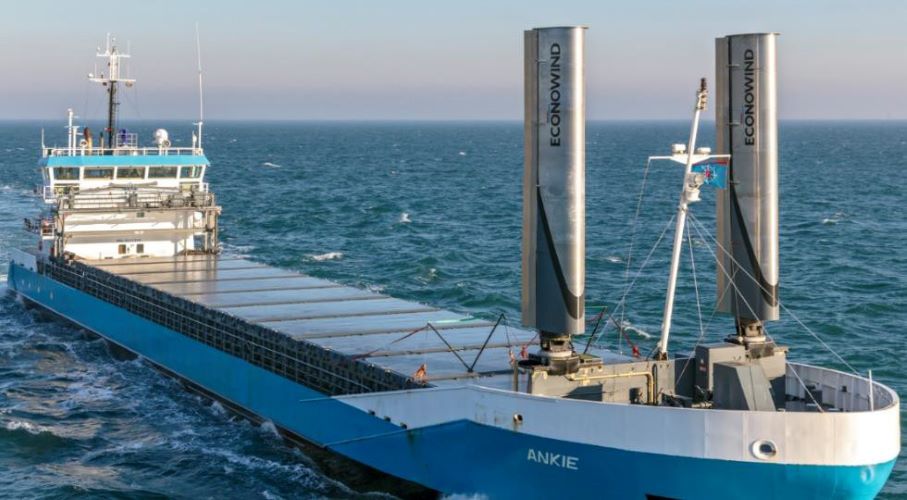
Wind-assisted propulsion in the marine industry represents a fascinating blend of traditional sailing principles and modern engineering innovation. This technology has gained significant attention in recent years as the shipping industry seeks more sustainable and cost-effective ways to power vessels. By harnessing the natural power of wind, ships can reduce their fuel consumption and environmental impact while maintaining efficient operations.
Understanding Suction Wings Suction wings represent an innovative approach to wind-assisted ship propulsion that combines traditional aerodynamic principles with active flow control technology. Unlike conventional sails or rigid wing sails, suction wings use a system of carefully positioned holes or slots along their surface through which air is actively drawn in or expelled. This unique design allows the wings to generate significant propulsive force even in relatively light wind conditions, making them particularly valuable for commercial shipping applications.
These specialized wings typically consist of a rigid or semi-rigid airfoil structure with an internal network of channels and pumps. The surface of the wing features numerous small openings that can be individually controlled to optimize airflow around the wing. This active control system allows suction wings to maintain efficient operation across a wider range of wind conditions compared to passive wind-assisted propulsion systems.
Suction sails are non-rotating wing-shaped sails with vents and an internal fan that creates suction, pulling in
a boundary layer of air around the wing for enhanced effect. The system was originally designed and deployed in the 1980s. The vertical structures are mounted onto the deck like rigid sails and rotor sails.
In contrast to rotor sails, their outer parts do not rotate to generate thrust. The orientation of the wings is adjusted automatically to the direction of the wind.The sails deliver optimal thrust at beam winds, while their thrust is practically zero at head and tail winds. The current height of suction wings ranges from 10-36 m. Two or four wings per ship is common but, in some instances, only one wing is installed.
Engineering Principles
The engineering behind suction wings involves sophisticated fluid dynamics concepts. The basic principle relies on boundary layer control, where the natural airflow around the wing is modified by actively removing or adding air through the wing’s surface. When air is sucked through the small openings on the wing’s surface, it helps prevent flow separation and maintains smoother airflow around the wing. This process is similar to how modern aircraft use various devices to control airflow and enhance lift.
The system works by creating a more favourable pressure distribution around the wing. By strategically removing air from certain areas and potentially adding it in others, suction wings can generate higher lift coefficients than conventional wing designs. This means they can produce more thrust for a given wing size, making them more efficient in terms of deck space utilization.
The internal structure of a suction wing includes several key components. Vacuum pumps or fans create the necessary pressure differential to draw air through the surface openings. A network of channels within the wing distributes this suction effect across the wing’s surface. Sophisticated control systems continuously adjust the suction patterns based on wind conditions, ship speed, and desired performance parameters.
Components
Suction wing sails are comprised of the below main components:
- Vertically installed wing incorporating the ventilator fan
- Ventilator system for the fan
- Folding mechanism (for folded systems)
- Hydraulic system & powerpack
- Control Panel and Electrical system
To control the airflow around the ‘thick’ foil-shape, a boundary layer suction is applied for which one or more Ventilators needs to be installed inside the suction wing profile. At the leading edge (the ‘nose’ of the egg-shaped cross-section) the airflow is accelerated leading to very low pressure on the top-left side of the profile and all along the suction-side.
It is an artificial way to reduce the drag coefficient of the wing profile while keeping the lift coefficient high, even as high as up to 7-8 depending on the angle of attack and the suction efficiency. The sizes can vary between 10 and 36 m tall.
The suction wing sail can develop quite high lift forces without any self-rotation mechanism, with relatively compact dimensions. They are fully automated and can be foldable in case of unfavourable wind conditions or during cargo operations.
Suction wing sails can be installed either in a containerized form or with a flat-rack or fixed on the deck. When a containerized system is considered then it can be installed as a simple container unit by fixing the system with straps to the hatch cover and plug the system to a 400V/32A plug.
It is expected that certain maintenance will be needed on the main bearing, the ventilator fan, the flap motor and the hydraulics, with most components being familiar/similar to other usual ship equipment.
Companies at Forefront
Companies Advancing the Technology Several innovative companies are working to develop and commercialize suction wing technology. eConowind, a Dutch company, has developed a unique suction wing system called the VentiFoil. Their design combines boundary layer suction with wing shapes optimized for maritime applications. The company has successfully installed their systems on several commercial vessels and reported significant fuel savings.
Bound4Blue, while primarily known for their rigid wing sails, has also conducted research into suction-enhanced wing designs. Their investigations have focused on combining traditional wing sail technology with active flow control systems to improve performance in marginal wind conditions.
MOL Techno-Trade, a subsidiary of Mitsui O.S.K. Lines, has been exploring suction wing technology as part of their broader efforts to reduce vessel emissions. Their research has included both standalone suction wings and hybrid systems that combine multiple wind-assisted propulsion technologies.
Different Types of Suction Wings
Suction wing technology has evolved into several distinct variants, each designed to address specific operational requirements. Fixed suction wings are permanently mounted structures that maintain their position and shape. These systems offer simplicity and reliability but may present challenges for vessels that need to navigate under bridges or operate in height-restricted areas.
Retractable suction wings can be raised or lowered as needed, providing greater operational flexibility. These systems typically use hydraulic or mechanical systems to adjust their position, allowing vessels to maintain full maneuverability in port while maximizing wind assistance at sea.
Hybrid suction wings combine active flow control with other wind-assisted propulsion technologies. Some designs incorporate both suction and blowing capabilities, allowing them to optimize airflow in different wind conditions. Others combine suction wings with traditional rigid wing sails or Flettner rotors to create integrated wind-assisted propulsion systems.
Latest Innovations
Recent technological advances have significantly enhanced suction wing capabilities. Advanced materials science has led to the development of new surface treatments and porosity control systems that improve the efficiency of air suction while reducing maintenance requirements. Some manufacturers have developed self-cleaning surface technologies that help maintain optimal performance in marine environments.
Digital control systems represent another area of innovation. Modern suction wing installations use sophisticated sensors and algorithms to continuously optimize their operation. These systems can predict wind patterns, adjust suction patterns in real-time, and coordinate with other ship systems to maximize fuel savings while maintaining vessel stability and safety.
Energy recovery systems have also been introduced to improve overall efficiency. Some designs capture and reuse the energy from exhaust air, while others integrate solar panels into the wing structure to power the suction systems. These innovations help reduce the energy cost of operating the suction systems.
Wind-Assisted Propulsion in the Marine Industry – Nautical Voice
Future Prospects
The future of suction wing technology appears promising as the maritime industry seeks more effective ways to reduce emissions and fuel consumption. Research and development efforts are focusing on several key areas that could further enhance the technology’s effectiveness and broaden its adoption.
Advanced manufacturing techniques are being explored to reduce production costs and improve system reliability. 3D printing and other additive manufacturing processes could allow for more complex internal channel designs and better integration of control systems. These improvements could make suction wing systems more cost-effective and easier to maintain.
Integration with autonomous shipping technology represents another exciting development path. Future suction wing systems might incorporate artificial intelligence and machine learning to optimize their performance automatically. These systems could analyze vast amounts of data about wind patterns, vessel performance, and route requirements to maximize fuel savings while maintaining schedule reliability.
New materials and smart surfaces are being developed that could revolutionize suction wing design. Shape-memory alloys and adaptive materials might allow wings to automatically modify their geometry based on wind conditions. Biomimetic surfaces inspired by natural phenomena could improve aerodynamic performance while reducing energy requirements for the suction system.
Economic considerations will likely drive continued innovation in this field. As carbon pricing mechanisms become more prevalent and fuel costs remain volatile, the business case for suction wing technology is expected to strengthen. This could lead to increased investment in research and development, potentially accelerating the pace of innovation.
The integration of suction wings with other clean technologies presents interesting possibilities for the future. Hybrid systems combining suction wings with hydrogen fuel cells, battery storage, or other renewable energy sources could create highly efficient vessels with minimal environmental impact. Some researchers are exploring ways to use the suction system for multiple purposes, such as ventilation or cargo hold conditioning.
In conclusion, suction wing technology represents a sophisticated approach to wind-assisted ship propulsion that offers significant potential for reducing maritime emissions and fuel consumption. As the technology continues to mature and evolve, it is likely to play an increasingly important role in the future of sustainable shipping. Ongoing research and development efforts, combined with growing environmental pressures, suggest that suction wings will become more prevalent in the coming years as part of the maritime industry’s transition to cleaner, more efficient operations.