Suppressing thruster tunnel drag to save energy and costs
Optimizing Ship Design Reducing Drag with Thruster Tunnels
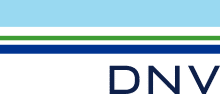
Shipbuilding and hydrodynamics experts at Fincantieri and DNV have collaborated closely to address drag caused by bow thruster tunnels, aiming to minimize hull resistance and reduce fuel consumption and carbon emissions.
When designing new cruise ships, Fincantieri engineers focus on maximizing fuel efficiency while maintaining reasonable newbuild costs and ensuring passenger comfort. With IMO decarbonization targets approaching, cruise ship operators will face higher fuel costs as zero-carbon fuels become necessary, along with additional expenses from carbon cap-and-trade schemes. Consequently, even minor hull design elements, such as the thruster tunnels in the bow section, have become crucial.
Optimizing Hull Form Around Thruster Tunnels
Thrusters are primarily used for lateral movement in port and for adjusting the vessel’s heading in specific navigational situations. However, for most of a voyage, thrusters remain inactive.
“Cruise ships have up to five bow thrusters,” explains Antonio Caizzi, Design Engineer at Fincantieri. “The discontinuity in the hull shape around the thruster tunnels, especially the rounded tunnel edges, causes local turbulence that increases hull resistance in water. This should be minimized by restoring the original geometry as much as possible.”
Joint Study with DNV Using Advanced CFD Analysis
Fincantieri developed several concepts to reduce drag and sought neutral verification from DNV using advanced computational fluid dynamics (CFD). They funded a joint study to determine if these solutions could improve ship efficiency.
“Fifteen years ago, saving one or two percent of fuel costs wouldn’t have attracted much interest, but now, with rising fuel and emissions costs, these savings are significant,” says Dr. Cosmin Ciortan, Principal Specialist and CFD expert at DNV. “Every percent of fuel saved can translate to cost savings, including carbon costs, which are no longer negligible.”
Traditional Designs and Shutters Are Insufficient
DNV’s extensive studies revealed the hydrodynamic effects and assessed Fincantieri’s solutions. Traditional methods, like simple metal grids, were found inadequate.
Installing shutters to close tunnel openings adds weight, complexity, and cost. “Shutters have been used on naval ships, but they require space and can cause noise and vibration, which are undesirable on a cruise ship,” says Caizzi. Fincantieri proposed an alternative solution.
CFD Investigation Into Thruster Tunnel Turbulence
Using a virtual hull model from Fincantieri, Ciortan’s CFD analysis pinpointed areas of significant resistance and flow correction needs. “We confirmed that traditional thruster tunnel configurations cause unwanted turbulence around the edges and inside the tunnel, resulting in lost energy,” says Ciortan.
The study focused on the forward part of the tunnel edge. “We found it sufficient to cover only the forward one-third of the tunnel,” says Caizzi.
A Cost-Effective Hydrodynamic Solution
Fincantieri’s patent-pending solution features a specially designed grid and a hinged, slotted deflector covering the forward portion of the tunnel. The grid bars extend axially, and the deflector opens when the thruster is activated, creating chambers of still water that shield the tunnel and guide flow towards the aft edge. “This reduces downstream turbulence significantly with minimal added steel,” says Caizzi. “It maintains an ideal thruster flow pattern, reducing noise and vibration, thus enhancing passenger comfort.”
This design is simple, requiring less maintenance and weight, while achieving the same results as a solid cover. It is available as an option for newbuilds or as a retrofit.
Advancing CFD Precision in Hydrodynamics
Detailed CFD studies have only recently become possible, and the industry was initially skeptical of CFD results. Over time, methods have been refined to deliver high-resolution hydrodynamic data, earning industry trust. “Our understanding of hydrodynamic effects has improved, reducing measurement error margins and enhancing our grasp of factors affecting fuel consumption,” says Ciortan.
DNV’s commercial codes are now robust, emphasizing the importance of quality data. Caizzi adds, “Using these powerful mathematical tools requires professional expertise, and we appreciate the strong support from DNV in this project.”